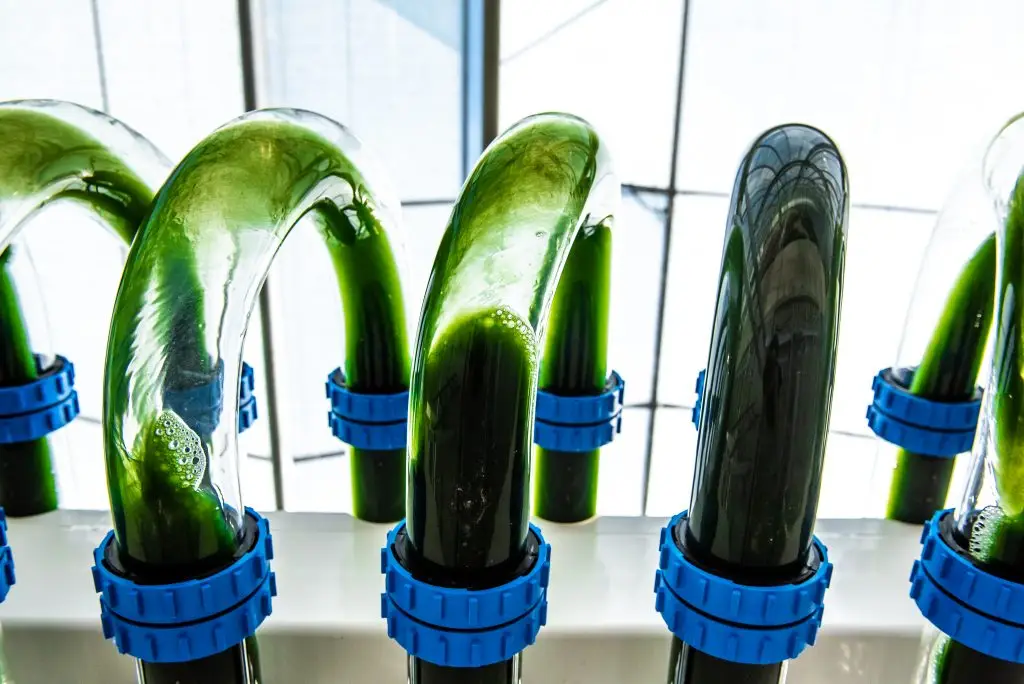
Photanol is dedicated to restoring balance on the planet by revolutionizing chemical production through circular practices. By optimizing cyanobacteria’s natural superpower of photosynthesis to absorb more CO2, adapting its metabolic pathways to produce a desired chemical. With the implementation of Lgem’s 25L bioreactor, Photanol has taken a significant leap towards scalability for industrial-sized production.
Challenge in upscaling
To gain traction within the chemical production industry, Photanol must provide a viable alternative without compromising quality, ensuring that desired carbon compounds can be produced on a large scale and at a low cost.
Hayco Bloemen, Principal Scientist Process Development: ” We are developing & optimizing our process to enable large-scale production, which bears elements from farming, biotechnology, and chemical engineering.”
Initially, Photanol cultivated its product in conventional 20L glass jars in their lab. However, this method was time-consuming, taking up to a month to yield results. Additionally, it lacked measurement points, had a higher risk of contamination, and half of the cases in the glass jars failed. Although relatively inexpensive, the low success rate made this method unsuitable for scaling up. “If the inoculation is not correct, there is no foundation to build upon.”
"We are developing & optimizing our process to enable large-scale production, which bears elements from farming, biotechnology, and chemical engineering."
Hayco Bloemen
Principal Scientist Process Development,
“Nothing so expensive as a failed experiment”
Hayco Bloemen
The Importance of Measurement and Control
Two scenarios were considered for the next step. The first involved a low-cost system using plastic bags. However, this approach did not improve results or expedite the process.
At this point, Photanol turned to Pieter Oostlander, bioprocess scientist at Lgem to discuss the second scenario, which involved using a reactor that could be measured and controlled, with a greater focus on the cultivation process rather than just the outcome. Despite being a more expensive option, “costs weren’t the primary consideration,” says Hayco, “Process performance in terms of speed, ability for process control & monitoring, and reliability was our main concern.” They sought a system that was fast, could be monitored and controlled, focused on hygiene, and minimised contamination risks. Lgem’s 25L bioreactor offered the desired features and the fact that it was steam-driven was also appealing. After consulting about these experiences, it turned out that these steam tests in fact had been done with Photanol’s steam generator, which we re-commissioned for this purpose
Having worked with Lgem before, Photanol knew they would receive the necessary support, high-quality equipment, and prompt troubleshooting assistance. Lgem was always available as a reliable sparring partner.
Breakthrough Results from the Start
The 25L bioreactor was delivered by the end of 2021, and it immediately yielded breakthrough results in terms of speed and production, by far surpassing Photanol’s previous experience with the conventional 20L glass jars, which could take up to a month to provide enough inoculum. Even outperforming our wish to provide inoculum within a week was surpassed: the first run provided enough biomass within half a week.
Over the course of one year, the process was further improved, a second 25L bioreactor was installed, allowing to do process development tests at this scale (next to inoculum production), which provided key insights for improving the larger scale pilot experiments
They even managed to skip another time-consuming step in the lab for the whole inoculation train, simplifying the whole inoculation process, while speeding it up and improving reliability, overall achieving a 10-fold rate improvement, and a 100% success rate.
Customized Tweaks for Optimal Results
In addition to utilising steam for sterilisation of the photobioreactor prior to inoculation, Photanol used Lgem’s best practices regarding contamination and made some additional tweaks to Lgem’s 25L system. Hayco: “We added a filter before the water bottle to prevent contamination, and also replace it regularly after consultation with Lgem.” The ability to clean all parts is a significant advantage of Lgem’s 25L system, as it allows to inoculate larger pilot reactors with a healthy and axenic inoculum. This has contributed to improve results in our larger pilot-scale reactors as well. On top of this the experiences of the 25L system translate well to larger pilot scale, and therefore it provides a valuable step for further process development.
Hayco Bloemen, Principal Scientist Process Development: “Nothing so expensive as a failed experiment”
Looking ahead, Photanol envisions an increased focus on hygiene and reduced production costs. These factors are crucial for the development of circular chemical production and the replacement of petrochemicals with sustainable, recyclable, and reusable chemicals. By continuously optimizing the Lgem’s 25L system and refining their expertise, Photanol strives to make even greater strides in scaling up and achieving commercial production on an industrial scale.
With ongoing support and collaboration from Lgem and other industry partners, Photanol is well-positioned to shape the future of sustainable chemistry. By pursuing a balanced planet and promoting the transition to a circular economy, Photanol remains committed to creating a cleaner and more sustainable future for all of us. Optimizing photosynthesis.