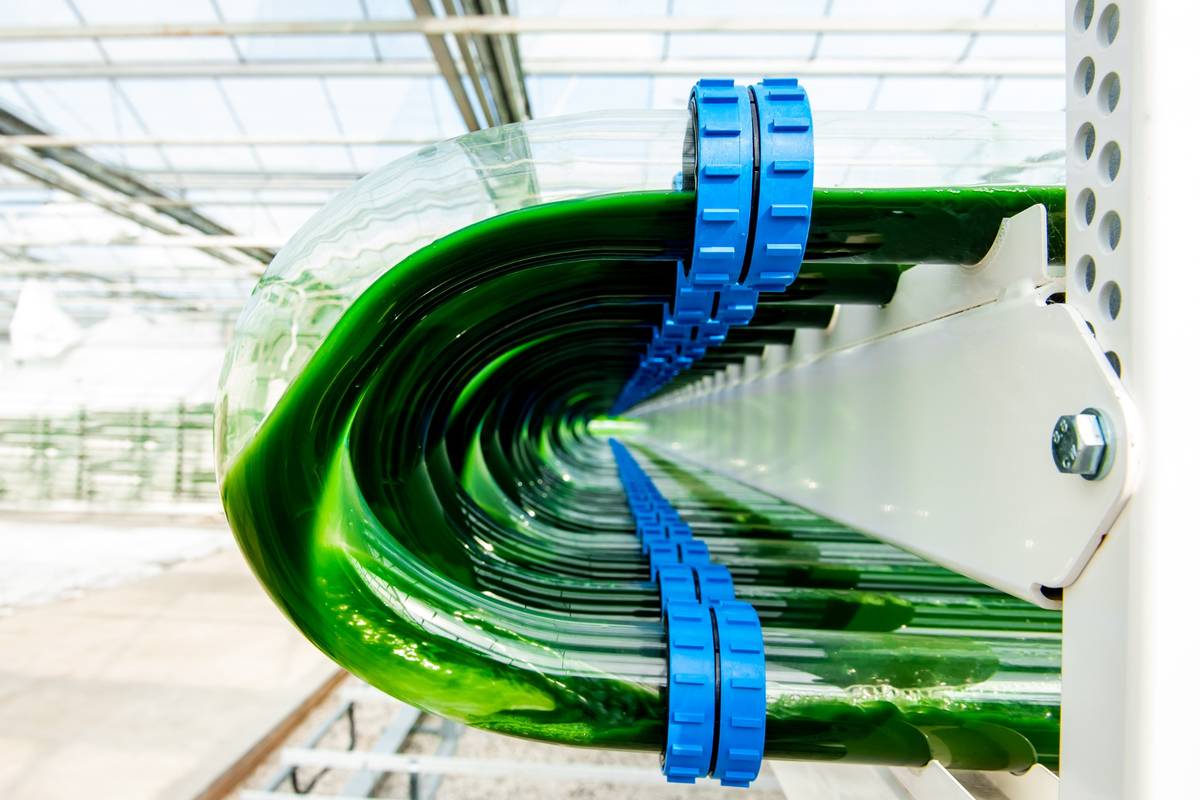
Scaling up algae production to an industrial level presents both opportunities and challenges. Achieving high productivity and consistent yield at scale demands a comprehensive approach that balances technology, operational efficiency, and economic considerations. Lgem’s photobioreactors (PBRs) are designed to navigate this complexity with advanced engineering, precision control, and proven operational strategies. This article provides an in-depth exploration of how producers can optimise Lgem PBR performance for high-density algae cultures, covering aspects from financial feasibility to downstream integration.
Economic considerations and operational efficiency
Large-scale algae cultivation hinges on economic viability. As production scales up, economies of scale reduce the cost per kilogram of biomass. While the productivity per litre may decline at larger volumes as control becomes more difficult, the overall operational efficiency improves significantly. Larger installations benefit from optimised energy consumption, bulk purchasing of nutrients, and enhanced use of infrastructure. Lgem’s closed PBR systems are engineered to maximise nutrient uptake and minimise losses, enabling cultivators to achieve higher cell concentrations with reduced waste output.
Although the initial capital investment for installing PBR technology can be substantial, long-term operational savings often justify the expenditure. Lower labour costs, reduced risk of contamination, and improved yield stability all contribute to faster return on investment. Moreover, financial incentives such as grants, subsidies, and industry-specific funding programmes are available in many regions, further supporting the economic feasibility of adopting Lgem’s systems.
Enhancing algae cultures through precision control and advanced automation
Consistent high-density cultivation requires stable and controlled growth environments. Lgem PBRs are equipped with integrated sensors that continuously monitor critical parameters, including temperature, pH, dissolved oxygen, and culture density. Real-time data collection allows for proactive adjustments, ensuring optimal conditions throughout the production cycle. For example, during periods of elevated temperatures, the system can automatically activate cooling mechanisms or adjust lighting intensity to mitigate thermal stress.
Remote monitoring capabilities enable operators to oversee multiple production sites simultaneously, ensuring rapid response to deviations without the need for constant on-site supervision. This level of automation not only enhances operational reliability but also reduces dependency on manual interventions, minimising the risk of human error. Automated nutrient dosing systems further ensure that algae cultures receive precise amounts of essential nutrients, maintaining optimal growth conditions and promoting consistent biomass quality.
Robust contamination management strategies
Contamination poses a significant risk in large-scale algae production, with potential to compromise entire batches and disrupt production schedules. Lgem’s closed-loop systems mitigate this risk through comprehensive filtration of incoming air, CO₂, and nutrient streams. Additionally, the use of validated cleaning-in-place (CIP) protocols ensures thorough cleaning of the entire system between production runs. These protocols typically involve a sequence of alkaline and acidic rinses, followed by disinfection with industry-approved chemicals, ensuring compliance with stringent hygiene standards.
Proactive monitoring plays a vital role in contamination prevention. Daily microscopic inspections, alongside regular checks of culture colour, odour, and growth rates, help detect early warning signs of contamination. Operators can implement corrective actions—such as targeted cleaning cycles or culture replacement—before the issue escalates, safeguarding overall system integrity and productivity.
Enhancing biomass yield and product consistency
Maximising biomass yield while maintaining product quality requires fine-tuning of growth parameters. Variables such as light intensity, photoperiod, temperature, and nutrient composition must be adjusted to align with the specific requirements of different algae strains. For instance, lipid accumulation for biofuel applications can be stimulated through controlled nutrient limitation, while high-protein biomass production for nutritional products may demand different growth conditions.
Lgem’s proprietary Wavywind® and Bubblebrush® technologies optimise mixing and gas exchange within the reactors, ensuring homogeneous distribution of nutrients and dissolved gases. This uniformity prevents dead zones and supports consistent cell growth across the entire culture volume. Efficient mixing not only enhances overall productivity but also improves the scalability of processes, allowing producers to replicate lab-scale results at industrial levels with minimal performance drop-off.
Streamlining downstream processing and integration
Efficient harvesting and downstream processing are critical to the profitability of large-scale algae production. High-density cultures reduce the volume of liquid that must be processed, improving the efficiency of dewatering and biomass collection. Techniques such as centrifugation and membrane filtration are commonly integrated with Lgem PBR systems, offering rapid and cost-effective biomass separation.
Maintaining uniform biomass quality throughout the production cycle is essential, particularly for applications in food, feed, pharmaceuticals, and nutraceuticals, where regulatory standards are stringent. Consistent cultivation parameters ensure that harvested biomass meets the required specifications for downstream processing, improving the yield and quality of extracted compounds such as proteins, lipids, or pigments.
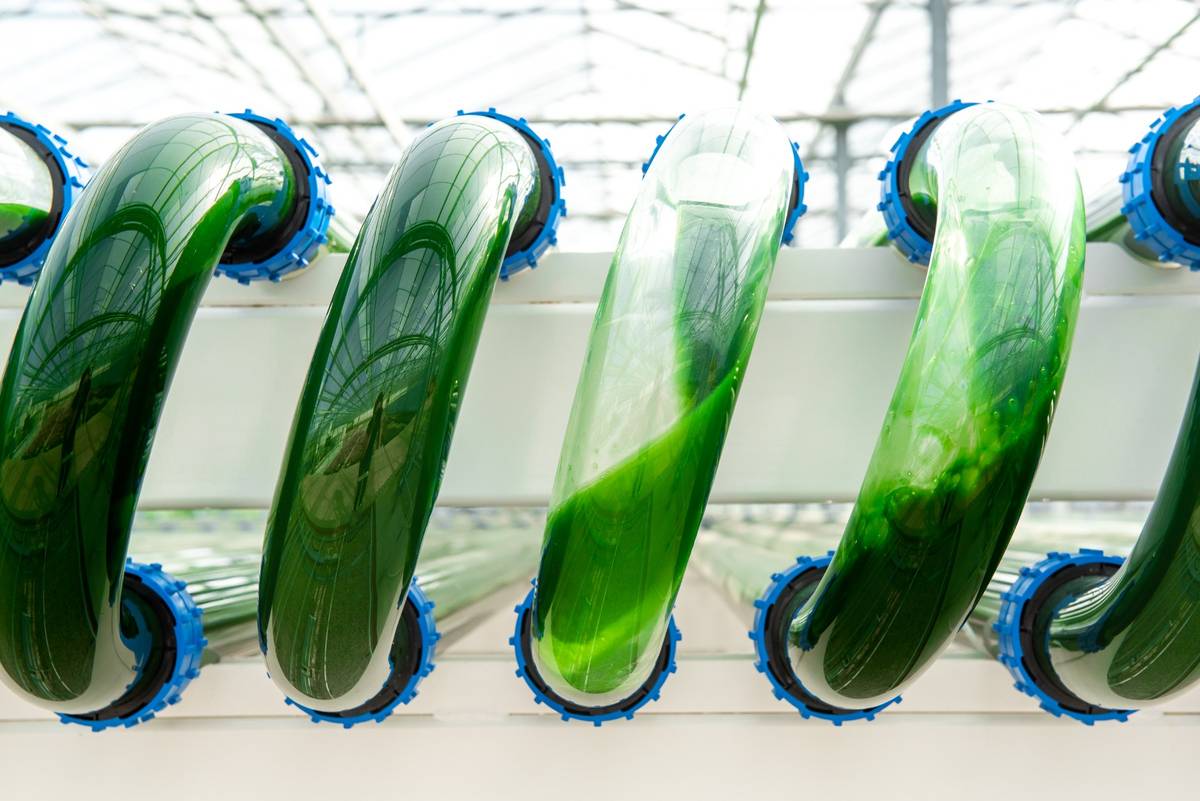
Our PBR systems offer this level of control, enabling researchers to fine-tune growth conditions for experimental purposes and producers to standardize processes for commercial production. Whether the goal is lipid-rich biomass for consumption or protein-dense strains for functional foods, these technologies prLgem’s modular reactor designs facilitate seamless integration with a wide range of downstream processing equipment, allowing producers to adapt their setups to evolving market demands. Whether targeting high-value nutraceutical products or bulk biofuel feedstocks, Lgem’s systems offer the flexibility needed to align production capabilities with end-user requirements.
Future-proofing algae cultures through innovation
The algae industry is rapidly evolving, with technological advancements continuously pushing the boundaries of what is possible at an industrial scale. Lgem remains at the forefront of these developments, investing in research to enhance automation, improve energy efficiency, and further reduce production costs. Emerging technologies, such as predictive analytics and artificial intelligence, promise to offer even greater control over cultivation processes, allowing for smarter decision-making and enhanced production outcomes for algae cultures.
As sustainability becomes an increasingly critical factor in global supply chains, algae’s role as a renewable resource for food, feed, and bio-based materials continues to grow. By adopting innovative solutions like those offered by Lgem, producers can not only meet current industry demands but also position themselves for long-term success in a competitive market.
By combining cutting-edge automation, robust contamination control, and a commitment to process optimization, Lgem’s photobioreactors empower algae producers to achieve reliable, scalable, and cost-effective production. With the right operational strategies, growers can maximise their production potential while meeting the stringent quality and sustainability standards of diverse application markets.